Laboratório de Materiais
O Laboratório de Materiais é o coração pulsante da engenharia e da construção civil.
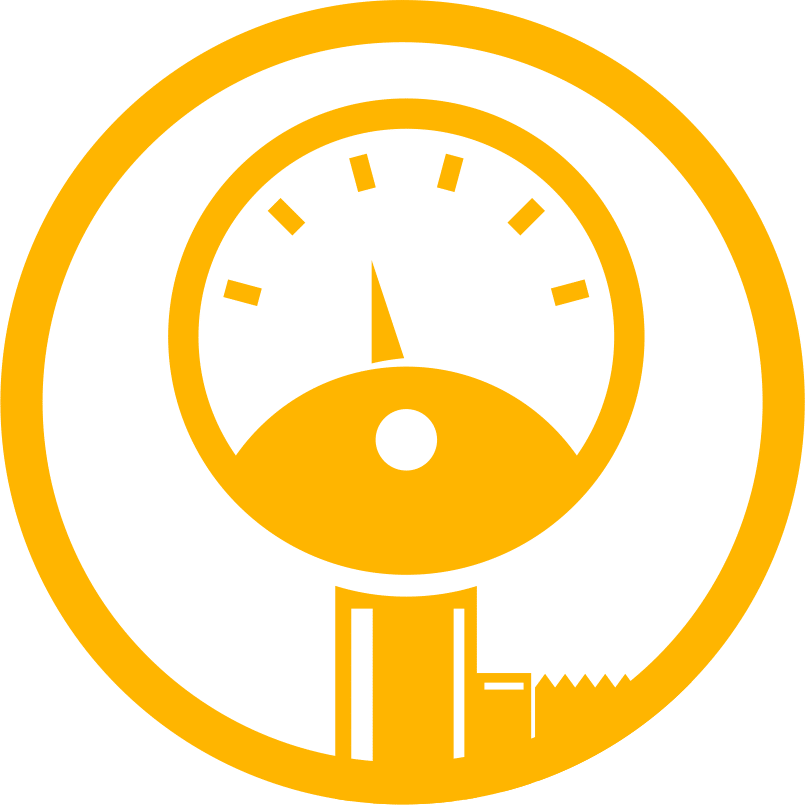
LABORATÓRIO DE MATERIAIS
A compreensão profunda dos materiais é essencial para enfrentar os desafios da construção moderna.
O Laboratório de Materiais
Desvendando a Ciência por Trás das Construções
O Laboratório de Materiais é o coração pulsante da engenharia e da construção civil. Nesse espaço dedicado à ciência dos materiais, a magia acontece: desde a análise minuciosa de componentes até a busca incessante por soluções inovadoras.
Equipado com tecnologia de ponta e uma equipe de especialistas altamente qualificados, o Laboratório de Materiais é o ponto de partida para edificações sólidas e duradouras. Aqui, ensaios e testes rigorosos são realizados para verificar a resistência, a durabilidade e a qualidade de cada elemento que compõe uma obra.
A compreensão profunda dos materiais é essencial para enfrentar os desafios da construção moderna. Do concreto ao aço, passando por cerâmicas, asfaltos e polímeros, o Laboratório de Materiais é o guardião do conhecimento que sustenta as construções do presente e do futuro.
Com uma abordagem precisa e confiável, o laboratório proporciona respostas às perguntas mais complexas. Ele fornece as ferramentas necessárias para otimizar projetos, garantindo a segurança e a eficiência nas estruturas que nos cercam.
Assim, quando você caminha pelas ruas, admira uma ponte majestosa ou desfruta de uma infraestrutura de qualidade, lembre-se que por trás dessas grandiosas realizações há a ciência, a dedicação e a expertise do Laboratório de Materiais.
Na Carlos Campos, nossa paixão pela excelência e nossa busca constante pelo avanço tecnológico impulsionam nossos serviços laboratoriais. Há mais de 50 anos, trabalhamos incansavelmente para fornecer dados precisos e soluções inovadoras, honrando o compromisso com a segurança e a qualidade das construções.
Seja em projetos de infraestrutura, obras civis ou empreendimentos arquitetônicos, o Laboratório de Materiais desempenha um papel fundamental para o progresso da engenharia e o bem-estar da sociedade. Afinal, ele é o espaço onde os sonhos ganham vida e onde a ciência se materializa em grandes realizações.
Sobre Laboratório de Materiais
O Laboratório de Materiais é o coração pulsante da engenharia e da construção civil. Nesse espaço dedicado à ciência dos materiais, a magia acontece: desde a análise minuciosa de componentes até a busca incessante por soluções inovadoras.
Ensaios que fazemos:
- Concreto
- Lajes de concreto
- Tubos de concreto
- Pré-moldados e artefatos de concreto
- Blocos de concreto, cerâmico e solo-cimento
- Telhas de concreto, cerâmica e fibrocimento
- Peças para pavimentação
- Argamassa
-
Argamassa colante
- Grau
- Agregados
- Aço
- Cimento
- Calda de cimento
- Gesso
- Revestimento cerâmico
- Pinos de ancoragem
- Dormentes
- Mourões
- Córdoba
- Parafusos
- Rochas
- Lastro Ferroviário
- Esclerometria
- Paquometria
- Extração de testemunhos

Ligue para uma cotação:
(62) 3204-2525
Nossos Serviços
Laboratório de Materiais
Controle Tecnológico de Solos e Asfalto
Laboratório do Ambiente Construído
Consultoria Técnica
Serviços em Obras
Serviços Especiais em Engenharia
Perguntas frequentes
Tem mais perguntas? Clique aqui e obtenha respostas para as perguntas frequentes!
Qual é a relevância do controle tecnológico aplicado aos agregados na indústria da construção?
Assegurar o desempenho ideal de uma estrutura e prevenir questões que poderiam comprometer a longevidade do projeto são os principais objetivos do controle tecnológico do concreto. Através desse procedimento, é possível analisar criteriosamente os parâmetros técnicos das amostras, permitindo a identificação precisa da qualidade e resistência dos materiais empregados.
Quais etapas são essenciais para o efetivo monitoramento e controle do concreto?
O processo é composto por três etapas fundamentais: Controle dos materiais utilizados e do processo produtivo, Monitoramento do concreto em seu estado fresco e Acompanhamento do concreto após sua cura e endurecimento.
Quais são os ensaios normatizados para o controle tecnológico do concreto?
De acordo com a NBR 12655 (ABNT, 2015), é fundamental realizar ensaios específicos para cada tipo e classe de concreto empregado em uma estrutura. Entre os principais ensaios destacam-se o teste de abatimento do tronco de cone, também conhecido como Slump Test, e o ensaio de resistência à compressão por meio de corpos de prova (CPs).
Por que o controle tecnológico do concreto é crucial?
O Controle Tecnológico do Concreto desempenha um papel fundamental em todas as etapas da obra. Juntamente com um projeto bem elaborado e uma execução cuidadosa, ele garante a segurança e a qualidade do empreendimento, evita gastos desnecessários e previne retrabalhos. O resultado final é a entrega de uma obra durável e a satisfação plena do cliente!
De quem é a responsabilidade pela realização do controle tecnológico do concreto?
A responsabilidade pela realização do controle tecnológico do concreto é compartilhada entre a concreteira e a construtora.
A concreteira tem a tarefa de realizar o controle de produção, garantindo que o concreto atenda aos requisitos técnicos e normativos estabelecidos. Porém, a construtora também possui um papel fundamental nesse processo. É de sua responsabilidade avaliar o concreto recebido, verificando se ele atende aos padrões de qualidade exigidos.
Vale ressaltar que diversos fatores podem interferir na qualidade do concreto desde a saída da central até o momento em que é aplicado na obra. Mudanças climáticas, transporte e eventuais atrasos na entrega no canteiro são apenas alguns exemplos.
Dessa forma, é essencial que a construtora realize inspeções e ensaios no concreto recebido, assegurando que ele esteja adequado para o uso na obra. Assim, a parceria entre a concreteira e a construtora é fundamental para garantir a qualidade e o desempenho do concreto na construção.
Como é feito o controle de qualidade dos materiais de construção?
O controle de qualidade dos materiais de construção é uma etapa crucial para garantir a excelência e a segurança das obras. Abaixo estão algumas das melhores práticas utilizadas na construção civil para esse fim:
- Planejamento: O controle de qualidade começa no planejamento da obra, definindo os padrões e especificações dos materiais a serem utilizados, bem como os critérios de aceitação.
- Controle de mão de obra: Além de garantir que os trabalhadores sejam qualificados e treinados, é fundamental acompanhar a execução das atividades para assegurar que estão sendo realizadas corretamente.
- Controle de materiais e fornecedores: Realizar uma rigorosa seleção de fornecedores confiáveis e com materiais de qualidade é essencial. O recebimento dos materiais deve ser inspecionado para garantir que estejam de acordo com as especificações.
- Avaliações internas: Realização de inspeções e ensaios periódicos durante todas as etapas da construção para identificar desvios e corrigi-los de forma rápida.
- Otimização dos processos: Buscar sempre aprimorar os métodos construtivos, com foco na qualidade e eficiência.
- Redução de custos e desperdícios: Evitar o desperdício de materiais e recursos, otimizando o uso dos insumos disponíveis.
- Aumento de produtividade: Buscar a eficiência na execução das tarefas, garantindo o cumprimento dos prazos e a qualidade do trabalho.
- Eficiência no controle de processos: Ter um sistema eficaz de controle de qualidade, com registros detalhados das etapas realizadas e resultados obtidos.
Essas práticas permitem um controle efetivo sobre os materiais utilizados na construção, desde a seleção dos fornecedores até a aplicação na obra. Dessa forma, é possível assegurar que a construção seja executada com materiais de qualidade, dentro dos padrões estabelecidos e em conformidade com as normas técnicas e regulamentações vigentes. Isso resulta em obras mais duráveis, seguras e com menor incidência de problemas, o que contribui para a satisfação dos clientes e o sucesso do empreendimento como um todo.
Quais os ensaios devem ser realizados no controle tecnológico dos agregados?
No controle tecnológico dos agregados, diversos ensaios são realizados para avaliar suas características e garantir sua qualidade e adequação ao uso na construção civil. Dentre os principais ensaios executados pelo laboratório durante a execução do projeto, destacam-se:
- Análise Granulométrica: Esse ensaio visa determinar a distribuição granulométrica dos agregados, ou seja, a proporção de partículas de diferentes tamanhos que compõem o material. Isso é importante para verificar se os agregados estão dentro dos limites granulométricos especificados pelo projeto.
- Massa Específica: A massa específica dos agregados é a relação entre a massa do material e o volume que ele ocupa. Esse ensaio é relevante para avaliar a densidade dos agregados e sua influência nas características do concreto.
- Teor de Material Pulverulento: O ensaio de material pulverulento verifica a quantidade de material fino e pulverulento presente nos agregados. O excesso desse tipo de material pode afetar a trabalhabilidade do concreto e sua resistência.
- Absorção: A absorção dos agregados indica a quantidade de água que os materiais são capazes de absorver. Esse ensaio é essencial para ajustar a quantidade de água a ser utilizada na mistura do concreto, evitando problemas como segregação.
- Coeficiente de Inchamento: O coeficiente de inchamento é a relação entre o volume do agregado solto e seu volume compactado. Esse ensaio é relevante para calcular o volume real dos agregados na mistura e obter proporções adequadas de materiais na produção do concreto.
Esses ensaios permitem uma caracterização completa dos agregados, fornecendo informações vitais para a correta dosagem e mistura dos materiais na produção do concreto. Além dos ensaios mencionados, outros também podem ser realizados, dependendo das especificidades do projeto e das normas técnicas vigentes. O controle adequado dos agregados é fundamental para assegurar a qualidade e a durabilidade das estruturas de concreto, bem como para evitar problemas durante a execução da obra.
Quantos MPa em 7 dias?
Nos ensaios de resistência do cimento CP IV conforme a norma ABNT - NBR 5736, espera-se que o concreto atinja uma resistência mínima específica em diferentes períodos de tempo. De acordo com a informação fornecida:
- Aos 3 dias, a resistência mínima estabelecida é de 10 MPa.
- Aos 7 dias, a resistência mínima estabelecida é de 20 MPa.
- Aos 28 dias, a resistência mínima estabelecida é de 32 MPa.
Portanto, ao final de 7 dias, espera-se que o concreto tenha atingido uma resistência de, no mínimo, 20 MPa. Isso significa que, após sete dias de cura e endurecimento, o concreto deve ser capaz de suportar uma carga de 20 megapascals (20 MPa) por unidade de área sem sofrer ruptura ou falha significativa. Esse é um parâmetro importante para garantir que o concreto esteja suficientemente resistente para suportar as cargas e tensões a que será submetido em sua aplicação na construção civil.
Quais são os principais ensaios do concreto?
Ensaios de concreto para estruturas já prontas
Além dos ensaios mencionados para concreto em estruturas já prontas, existem também ensaios importantes realizados em diferentes fases da produção do concreto, desde a sua elaboração até o controle de qualidade em obras. Abaixo estão alguns dos principais ensaios do concreto:
- Ensaio de Abatimento do Tronco de Cone (Slump Test): Mede a consistência do concreto fresco, indicando a sua trabalhabilidade e influenciando na facilidade de colocação e adensamento.
- Ensaio de Resistência à Compressão: Avalia a resistência do concreto endurecido, garantindo que ele atinja os valores mínimos requeridos para suportar as cargas projetadas.
- Ensaio de Moldagem e Cura de Corpos de Prova: São corpos de prova cilíndricos ou cúbicos retirados do concreto fresco, que permitem avaliar a sua resistência ao longo do tempo.
- Ensaio de Retração e Expansão: Mede a variação volumétrica do concreto em função do tempo, auxiliando no controle de possíveis deformações e fissuras.
- Ensaio de Carbonatação: Analisa a profundidade de penetração de dióxido de carbono no concreto, verificando a sua durabilidade e resistência a ambientes agressivos.
- Ensaio de Teor de Umidade: Determina a quantidade de água presente nos agregados, que influencia diretamente nas proporções da mistura do concreto.
- Ensaio de Absorção de Água: Mede a capacidade do concreto de absorver água, influenciando em sua durabilidade e resistência à deterioração.
- Ensaio de Resistência à Tração na Flexão: Avalia a resistência do concreto à tração, que é importante principalmente em elementos estruturais submetidos a flexão.
- Ensaio de Densidade e Massa Específica: Mede a densidade e massa específica do concreto, importantes para determinar as proporções dos materiais na mistura.
- Ensaio de Análise Granulométrica dos Agregados: Analisa a distribuição granulométrica dos agregados, fundamental para uma mistura adequada e homogênea do concreto.
Esses ensaios são fundamentais para garantir a qualidade e a segurança das estruturas de concreto, permitindo que sejam projetadas e executadas de forma confiável e durável ao longo do tempo.
O que é o FCK do concreto?
Na verdade, a informação fornecida sobre a tradução da sigla FCK (Feature Compression Know) para "Resistência Característica do Concreto à Compressão" não está correta. A sigla FCK, na engenharia civil e no contexto do concreto, representa o "Fator de Resistência Característica". É uma nomenclatura em português, não uma tradução do inglês.
O FCK é um parâmetro fundamental no dimensionamento de estruturas de concreto, pois se refere à resistência característica do material à compressão, ou seja, é o valor que representa a resistência média que uma série de corpos de prova de concreto deve atender para que haja uma probabilidade estabelecida de não ocorrer falha. Essa probabilidade está relacionada à segurança estrutural e é definida por normas técnicas e regulamentações.
Por exemplo, quando se especifica que um concreto tem FCK 30 MPa, significa que a resistência característica à compressão desse concreto é de 30 megapascals (MPa). Os valores do FCK variam de acordo com as necessidades e especificações de cada projeto, garantindo que a estrutura seja capaz de suportar as cargas e solicitações previstas ao longo de sua vida útil com um nível adequado de segurança.
Quais ensaios são utilizados para medir a resistência do concreto?
Correto, o ensaio mais utilizado para medir a resistência do concreto é o ensaio de resistência à compressão, também conhecido como ensaio de compressão ou ensaio de ruptura. Esse ensaio é padronizado e amplamente empregado para determinar a capacidade do concreto suportar cargas de compressão antes de entrar em colapso.
No ensaio de resistência à compressão, corpos de prova cilíndricos ou cubos de concreto são moldados a partir da mistura utilizada na construção. Esses corpos de prova são submetidos a uma carga crescente até o ponto de ruptura. A resistência à compressão é então calculada dividindo a carga máxima suportada pelo corpo de prova pela área da seção transversal.
Além do ensaio de resistência à compressão, existem outros ensaios que também podem ser usados para medir a resistência do concreto em diferentes contextos ou para verificar propriedades específicas do material, tais como:
- Ensaio de resistência à tração por compressão diametral: Mede a resistência do concreto à tração indireta.
- Ensaio de flexão: Avalia a resistência do concreto à flexão e à tração direta.
- Ensaio de ultrassom: Utiliza ondas sonoras para avaliar a homogeneidade e as propriedades do concreto, incluindo possíveis falhas ou vazios.
- Ensaio de esclerometria: Mede a dureza superficial do concreto, relacionando-a com sua resistência.
- Ensaio de arrancamento (pull-out): Avalia a aderência entre o concreto e uma barra de aço.
Cada ensaio tem sua importância em diferentes situações e pode fornecer informações valiosas sobre a qualidade e a resistência do concreto em obras e estruturas.
Quantos corpos de prova devem ser moldados?
O número de corpos de prova que devem ser moldados pode variar dependendo das normas e especificações adotadas em cada projeto e país. No trecho citado, menciona-se que devem ser retirados 4 corpos de prova de cada caminhão de concreto que chega à obra. Isso significa que, para cada carregamento de concreto proveniente do caminhão betoneira, devem ser moldados 4 corpos de prova.
Esses corpos de prova são moldados para representar o concreto utilizado em diferentes partes da estrutura, como fundações, pilares, vigas ou lajes. É uma prática comum e importante no controle de qualidade do concreto, pois permite verificar se o concreto atinge a resistência desejada dentro do tempo de cura necessário. Os corpos de prova são submetidos a ensaios de resistência à compressão em laboratório, nos tempos de cura adequados, para avaliar a qualidade e a resistência do concreto.
Vale ressaltar que a quantidade de corpos de prova e os procedimentos para moldagem, cura e ensaio podem variar conforme as especificações do projeto, as normas técnicas adotadas e as exigências específicas da obra. O acompanhamento rigoroso do processo de moldagem e ensaio dos corpos de prova é essencial para garantir a qualidade e a segurança das estruturas de concreto.
Como é feito o teste de Slump do concreto?
O teste de Slump, também conhecido como ensaio de abatimento do concreto, é um procedimento padrão para avaliar a consistência do concreto fresco. Ele é utilizado para determinar a fluidez e a trabalhabilidade do concreto antes de ser colocado nas formas da estrutura. O teste é realizado da seguinte maneira:
- Preparação do molde: Um molde confeccionado em metal é utilizado para o ensaio. Ele tem a forma de um tronco de cone com medidas específicas. O molde é colocado sobre uma base rígida e nivelada.
- Preenchimento do molde: O concreto fresco é cuidadosamente colocado no molde em três camadas iguais. Cada camada é compactada com o auxílio de uma haste metálica para garantir que não haja vazios de ar.
- Remoção do molde: Após o preenchimento, o molde é cuidadosamente levantado e retirado verticalmente de forma rápida e suave, deixando o concreto livre para se assentar.
- Medição do Slump: A altura do concreto após a remoção do molde é medida em relação à altura original do molde. Essa diferença de altura é chamada de "abatimento" ou "slump". Ela é uma medida da consistência e da plasticidade do concreto fresco.
O valor do Slump é expresso em centímetros e indica o grau de deformação que o concreto sofreu devido ao seu próprio peso. Concretos com diferentes finalidades e aplicações têm requisitos específicos para o valor do Slump, e esses valores são estabelecidos em normas técnicas.
O teste de Slump é uma ferramenta importante para garantir que o concreto esteja com a consistência adequada para ser aplicado na obra, evitando problemas durante a concretagem e contribuindo para a qualidade da estrutura final.
Qual a resistência do concreto em 7 dias?
A resistência do concreto em 7 dias é de aproximadamente 65% da resistência esperada em 28 dias. Isso significa que, após sete dias da concretagem, o concreto atinge cerca de 65% da sua resistência máxima.
Vale ressaltar que a resistência do concreto aumenta com o passar do tempo, devido ao processo de hidratação do cimento. Nos primeiros dias após o vazamento, o concreto ganha resistência rapidamente, como mencionado na informação fornecida. Em três dias, já alcança cerca de 40% da resistência final esperada, e em 14 dias, cerca de 90%.
Claro! Abaixo está uma tabela com as informações sobre a resistência do concreto em diferentes idades, com base nos dados fornecidos anteriormente:
Contudo, é importante lembrar que a resistência do concreto pode variar de acordo com diversos fatores, como a proporção e qualidade dos materiais utilizados, o tipo de cimento, as condições de cura, a temperatura e a umidade do ambiente, entre outros. Portanto, realizar ensaios específicos para medir a resistência do concreto em diferentes idades é fundamental para garantir sua adequação aos requisitos do projeto e das normas técnicas.
Como é feito o controle tecnológico do pavimento em campo?
O controle tecnológico do pavimento em campo envolve uma série de ensaios e verificações que têm como objetivo garantir a qualidade e o desempenho do asfalto utilizado na construção das vias. Esses ensaios são realizados por profissionais capacitados e em conformidade com normas técnicas específicas. Abaixo estão algumas das etapas e ensaios mais comuns no controle tecnológico do pavimento:
- Coleta de Amostras: São coletadas amostras representativas dos materiais utilizados na pavimentação, como agregados, ligantes asfálticos e misturas asfálticas. A coleta é feita de forma cuidadosa para garantir a representatividade dos materiais.
- Caracterização dos Materiais: Os materiais coletados são submetidos a ensaios de caracterização, nos quais são determinadas suas propriedades físicas e mecânicas. Essas informações são essenciais para a formulação da mistura asfáltica mais adequada para o pavimento.
- Ensaio Marshall: É um dos ensaios mais importantes para a determinação das características e resistência da mistura asfáltica. Nele, são moldados corpos de prova de asfalto compactado que serão submetidos a cargas de compressão e análises de estabilidade e fluência.
- Ensaio de Compactação: Esse ensaio avalia a densidade do asfalto compactado em diferentes teores de umidade e níveis de compactação. Isso é importante para garantir que a mistura asfáltica alcance a densidade adequada para suportar as cargas do tráfego.
- Verificação da Espessura: É fundamental medir a espessura do pavimento asfáltico aplicado para garantir que esteja de acordo com o projeto e as normas técnicas estabelecidas.
- Controle de Temperatura: O controle da temperatura é importante para garantir a boa trabalhabilidade do asfalto durante a aplicação, evitando problemas como segregação e falhas na compactação.
- Verificação de Outras Características: Além dos ensaios mencionados, outras características do pavimento asfáltico, como aderência, resistência à tração, durabilidade e textura, também podem ser avaliadas dependendo das especificações do projeto.
O controle tecnológico do pavimento em campo é uma etapa crucial para garantir a qualidade, a segurança e a durabilidade das vias. Através desses ensaios e verificações, é possível assegurar que o pavimento atenda aos padrões técnicos e seja capaz de suportar as solicitações do tráfego, proporcionando uma boa condição de rolamento para os usuários.
Quais os ensaios devem ser realizados no controle tecnológico do cimento Portland pavimentação?
O controle tecnológico do cimento Portland para pavimentação envolve uma série de ensaios que visam garantir a qualidade e o desempenho do cimento utilizado na produção de concreto asfáltico. Esses ensaios são realizados de acordo com as normas técnicas, sendo a NBR-7215 uma das principais referências. Abaixo estão alguns dos ensaios mais comuns realizados no controle tecnológico do cimento Portland para pavimentação:
- Ensaio de Resistência à Compressão: Nesse ensaio, corpos de prova de argamassa normal de cimento e areia, na proporção de 1:3 em peso, são moldados e submetidos a cargas de compressão. As resistências médias desses corpos de prova devem atender aos valores especificados na Tabela 2 da Norma NBR-7215.
- Análise Química: Através da análise química, são verificados os teores de componentes químicos do cimento, como sílica, alumina, ferro, cálcio e outros elementos, garantindo que estejam dentro das especificações estabelecidas pelas normas.
- Finura: O ensaio de finura avalia o grau de moagem do cimento, sendo um fator importante para a sua reatividade e influência nas propriedades do concreto asfáltico.
- Tempo de Pega: Esse ensaio determina o tempo necessário para o cimento atingir determinada consistência após a adição de água, o que influencia o processo de aplicação do concreto asfáltico.
- Expansibilidade: Verifica a expansão do cimento em determinadas condições, pois expansões excessivas podem comprometer o desempenho do concreto asfáltico.
- Perda ao Fogo: Mede a quantidade de material volátil presente no cimento, o que pode afetar suas propriedades físicas e químicas.
É importante ressaltar que os ensaios e especificações podem variar de acordo com as normas vigentes e as especificações do projeto. O controle tecnológico do cimento Portland para pavimentação é fundamental para garantir a qualidade do concreto asfáltico e, consequentemente, a durabilidade e o desempenho adequado das vias pavimentadas.
O que é controle de material?
O controle de material é uma prática essencial no gerenciamento de suprimentos e estoques em uma empresa. Trata-se da aplicação de métodos e procedimentos sistemáticos para garantir que os materiais necessários para a produção ou execução de um projeto sejam fornecidos de acordo com os requisitos estabelecidos, sejam eles de qualidade, custo e prazo de entrega.
O objetivo principal do controle de material é assegurar que os materiais adquiridos atendam aos padrões de qualidade esperados, estejam em conformidade com as especificações técnicas e sejam entregues dentro dos prazos acordados. Isso envolve a verificação da qualidade dos materiais recebidos, a rastreabilidade de cada item, o controle de estoque e a rejeição de itens que não estejam de acordo com os padrões estabelecidos no contrato ou acordo com o fornecedor.
Além disso, o controle de material também inclui o monitoramento de estoques para evitar faltas ou excessos, otimizando assim os níveis de inventário e evitando gastos desnecessários. Essa prática é de extrema importância para garantir a continuidade das operações da empresa, evitar perdas financeiras e manter a satisfação dos clientes ao fornecer produtos ou serviços de alta qualidade, no tempo certo e ao menor custo possível.
Em resumo, o controle de material é uma abordagem estratégica para gerenciar os suprimentos e garantir que os materiais utilizados nas atividades da empresa atendam aos padrões de qualidade, sejam economicamente viáveis e estejam disponíveis no momento necessário. Isso contribui para a eficiência operacional, a redução de riscos e a satisfação dos clientes.
Entre em Contato
>TELEFONE
(62) 3204-2525
lab@carloscampos.com.br
>Endereço
Av. São Francisco, 535 - Santa Genoveva, Goiânia - GO, 74670-010
